Tracking The Costs Of The Corrosion Epidemic
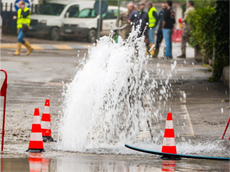
Environmental Catastrophe
The burden of old technology materials is not limited to the cost of repairing and replacing failed pipelines. It includes the cost of losing treated water from leaking systems. All told, leaking pipes lose some 2.6 trillion gallons of drinking water every year, or 17% of all water pumped in the United States. This represents $4.1 billion in wasted electricity annually. In many distribution systems, the amount of water lost or unaccounted for can be as high as 40 to 50 percent. Ninety percent of lost water costs are corrosion-related.
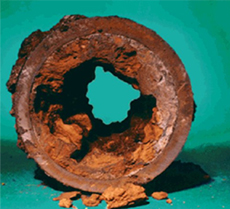
Tuberculation
Would you drink water from this pipe?

Clean and Sustainable
PVC pipe’s smooth surface equals clean and sustainable water delivery.
Resources

Corroded Iron Pipe Samples from Flint, MI
Municipalities with corrosion issues could be exposing their customers to potential public health and safety issues.
Why So Many Water Main Breaks?
Corrosion, leaks and breaks in old-technology pipe materials are degrading our water delivery and sewage treatment systems, which are critical to public health and the environment.
According to a 2023 Utah State University report North America experiences 710 water main breaks a day, totaling $2.6 billion in annual repair costs. This doesn’t include the high costs of emergency equipment, depleted water supply, traffic disruptions, and lost work time. Experts note that corrosion is the leading cause of this water main break epidemic.
Corrosion is a significant drag on the economy, costing U.S. drinking water and wastewater systems over $50.7 billion annually, or more than $1 trillion dollars over the next twenty years. Not only is this cost calculated in terms of water main break repair, but also in terms of lost water, replacement of corroded pipes and implementation of corrosion-mitigation measures, which are ineffective since they only delay an unavoidable outcome.
Today’s corrosion crisis is due to the materials used in America’s underground pipe networks over the last 100 years. At first, cast iron was used, with ductile iron gradually replacing it. Both now suffer from the ravages of corrosion.
The American Society of Civil Engineers has consistently given poor marks to the nation’s public drinking and wastewater systems, saying hundreds of billions must be spent over the next two decades for upgrades and replacements.
Taxpayers are fed up. Local governments are scrambling for solutions.
A Public Health Concern
Tuberculation is a form of internal corrosion and bio-film contamination which develops in iron pipes and restricts water flow. It can be a breeding ground for bacteria.
The town of Walkerton, Ontario provides a case in point. In 2000, E-coli had infiltrated the municipality’s iron-pipe water network, and purging it from the system was extremely difficult. Only after repeated and costly flushing with super-chlorination was the piping system safe to use again.
Unlike iron pipe, PVC pipe is not affected by tuberculation. Its smooth, non-corrosive surface stays clean even after decades. An ISO Standard 14025 Environmental Product Declaration conducted for PVC water and sewer pipe, certified by global health organization NSF International, confirms the safety of PVC water pipe: “No known chemicals are released into the water system. No known toxicity effects occur in the use of the product.”
Today, Walkerton, now part of the Municipality of Brockton, is replacing its iron pipes with PVC. In fact, it’s the only material the community now uses in its water system. Says Colin Saunders, Brockton’s utilities manager, “With PVC pipe, I don’t have concerns about corrosion, tuberculation or water main breaks, and this means lower maintenance costs and a longer lasting piping network.”
Environmental Impacts of Iron Pipe Made from Recycled Automobiles
It is important to critically examine recycling claims. Ductile iron (DI) pipe manufacturing, which uses metals from recycled automobiles, releases a host of additional chemicals such as lead, mercury, manganese, zinc, chromium compounds, trimethylamine, xylene, methanol and phenol compared to iron pipe made from virgin iron ore. The production of PVC pipe using virgin material is less energy intensive than DI pipe using recycled materials, resulting in fewer environmental impacts for water infrastructure projects. It is therefore critical to review using a life cycle data perspective, which may in fact indicate even greater impacts. When examining embodied energy impacts, the cradle-to-gate stage (raw material supply, transport and manufacturing) of DI pipe production exceeds the embodied energy of the entire life cycle of the equivalent PVC pipe. Moreover, piping materials such as polyethylene (HDPE) and prestressed concrete cylinder pipe (PCCP) also represent greater impacts, even when not accounting for replacement of failed piping systems.
The Solution: PVC Pipe
While certain pipe manufacturers continue to explore “solutions” to corrosion – because their materials are affected by it – PVC remains indisputably resistant to it.
PVC pipe is a proven and extremely durable alternative to traditional corrosion-prone pipe materials. Recognized by state, national and international agencies and standards organizations, it has been a benchmark since it was introduced in the U.S. sewer, water and drainage markets in the 1950s.
Over two million miles of PVC water and sewer pipe are currently in service. A review by Engineering News Record in 1999 found PVC for water and sewer pipe to be one of the top twenty engineering advancements in more than a century.
An American Water Works Association Research Foundation study confirms the life expectancy of PVC pipe to be in excess of 110 years.
PVC’s cost-effectiveness and sustainability are important qualities that city and local lawmakers should be considering–and taxpayers should be demanding.
LCA for PVC Pipe
Life Cycle Assessment of PVC Water and Sewer Pipe and Comparative Sustainability Analysis of Pipe Materials Report
Comparative analysis and environmental review of underground piping shows PVC pipe has fewer environmental impacts and life cycle costs over a 100-year life.
Click here for report.
PVC Pipe Low Monetized Carbon Footprint
If carbon output for cradle-through-installation were penalized for 8-inch PVC and ductile iron (DI) equivalent pipes at a functional length of 100 feet, PVC would be ranked lowest at $25 or $35 (depending on pressure class) compared to DI pipe at $225.
So Why Aren’t We Using PVC More Widely?
Outdated procurement rules in some municipalities ignore proven materials like PVC pipe. Closing bids to qualified products prevents informed decisions from being made, resulting in higher costs.
“The traditional habit of using one or two pipe materials exclusively is no longer satisfactory, local officials need to compare all proven pipe materials,” says Schenectady (NY) Mayor Brian Stratton, co-chair of the U.S. Conference of Mayors Water Council:
Since pipe is the largest component of a water utility’s assets, it’s critical that steps be taken to ensure its long-term sustainability, which will help utilities hold the line on costs.
PVC is the most cost-effective and durable piping material available today, and procurement practices should be reformed to ensure it helps solve the corrosion crisis in every municipality.
Our country’s underground infrastructure is at a crossroads. The time has come to put an end to the corrosion crisis and include PVC pipe in all municipal bids for underground infrastructure.
Latest News
Water Main Break Data
A study by the National Research Council (NRC) of Canada reported that the average break rate per 100 miles of pipe for ductile iron is 15.87. PVC exhibited only 1.17 breaks per 100 miles of pipe. The NRC report shows that ductile iron pipe breaks 13.57 times more than PVC pipe. This difference in break rates results in significant repair cost differences for PVC and ductile iron.
Comprehensive Study
Water Main Break Rates in the USA and Canada
Utah State University, Buried Structures Laboratory
Major Findings:
- PVC pipe has the lowest overall failure rate when compared to cast iron, ductile iron, steel and asbestos cement pipes;
- Corrosion is a major cause of water main breaks;
- Newer, thinner-walled ductile iron pipe is experiencing failures more rapidly than older cast iron pipes.
According to Utah State University, from 2012 to 2018:
- In North America, water main breaks have increased by 27%
- Asbestos cement pipe breaks have increased by 46%
- Cast iron pipe breaks have increased by 43%
- Ductile iron (DI) pipe failure rates have increased by 13%
- PVC pipe breaks have decreased by 10%
Water Pipe Break Rates, 2012 -2018
Transparent EPD
Find out how to objectively evaluate sustainability and environmental claims for underground infrastructure. Click here for technical paper.